2015 will be an unusual year for the executives at the Freudenberg Sealing Technologies facility in Bristol, NH as they experience the satisfaction of saving more than $1,100,000 in energy costs per year as a result of a plant heating system overhaul.
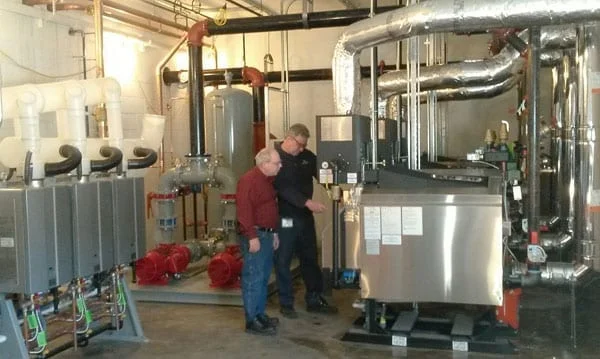
Freudenberg plant Engineer Rene Lefebvre and IMEC Senior Technician Mike Lawrence reviewing the operation of the new hot water boiler plant.
With the assistance of the mechanical engineering design/build firm IMEC in Ayer, MA, the Freudenberg factory’s legacy system, which employs obsolete high pressure steam boilers and #6 fuel oil, is being scrapped in favor of leading-edge design and technology. The plant’s entire heating load will be replaced with efficient liquefied natural gas (LNG), initially phased in by employing propane as a bridge fuel. The improvements will result in fuel savings of approximately $1,100,000 per year, electrical savings of $70,000 per year, and utility company rebates to defray costs. Carbon emissions from the facility will be reduced by an extraordinary 4,000 tons per year.
Many functional inefficiencies of the old system are being addressed: a substantial plant air negative condition, heating and cooling controls, and excessive maintenance costs. Problematic regulatory issues are also being eliminated, including #6 fuel emissions, on-site fuel storage, and boiler certification requirements.
SYSTEM DESCRIPTION
IMEC will replace 34 rooftop units, currently utilizing DX air conditioning and either steam or electric heat, with new high-efficiency gas HVAC units. The waste heat from the factory’s air compressors will be captured and utilized. Steam production loads and a portion of the existing steam heating load are being converted and served by a high efficiency gas hot water system.
To capture the 1,200,000 BTU/HR available from existing air compressors, IMEC has designed a special heat recovery coil that takes advantage of the available glycol temperature and converts it into usable heat. Select units in the factory will be retrofitted with these coils. The coils will become the primary source of heat, augmented with gas heat when the heating requirements increase. This approach maximizes the number of hours per year of free heat. Using the heat from the air compressors also reduces the load placed on the facility’s cooling towers, which will reduce cooling energy, evaporative water usage, and chemical treatment costs.
In addition to the energy and maintenance savings, climate control of the factory and offices will be much improved.
“It’s gratifying to see the remarkable impact this project will have on Freudenberg’s energy consumption and reduced carbon footprint,” says Joe D’Ambrosio, president of IMEC. “It showcases our ‘concept to commissioning’ full-service approach versus the alternative of hiring separate firms who cannot deliver equal speed, efficiency, and value. The project took 3 years of planning to come to fruition; it’s a perfect example of our commitment to forming long-term full-service partnerships with customers: to model concepts, devise creative solutions, engineer, execute, and push the button at the end.”
The project in now underway is expected to be operational by August 2015.
Complimentary Energy Efficiency Evaluation
SPECIAL OFFER
Learn about how our scientific approach to sustainable mechanical engineering will take your facility into a future of ultra efficiency.

Our engineers will dramatically improve your plant efficiency and help you take advantage of utility company rebates to cover a portion of the cost.
Through a combination of generous utility company rebates and IMEC’s high-efficiency engineering solutions, you’ll realize the benefits of streamlined mechanical systems that produce huge annual power savings.
We recently completed a project that is saving a customer over $1,100,000, annually.
Even if you don’t think you need a new mechanical system, it’s likely that we will discover a facet of your facility’s efficiency that can be improved dramatically. As an Authorized National Grid Project Expeditor, we also manage the utility rebate process for you.
Submit this form to receive your Complimentary Energy Consultation and Systems Evaluation:
- Plant walkthrough
- Identification of energy-saving projects
- Estimated ROI / Payback time
- Projected utility company rebates
An IMEC sales engineer will contact you to arrange a Complimentary Energy Consultation and Systems Evaluation.