Energy Efficiency Case Study
Award-winning custom-engineered and modified air compressor co-gen system achieves multiple benefits at Cains Foods
Project Overview
Cains originally contacted IMEC to aid in the selection and installation of a new air compressor. During our facility assessment, we also identified that the facility was running out of hot water during high demand usage. We suggested a co-generation solution.
Solution
We chose a 125 HP variable speed drive air-cooled air compressor coupled with a thermal mass cycling refrigerated air dryer. The goal of the compressor system was to increase electrical efficiency in the generation of the compressed air. We then modified the compressor in our laboratory to achieve 100% heat energy reclamation into a hot water supply.
An additional benefit to transferring the heat load into the hot water generation was the elimination of the cooling load required by the 5 HP on-board compressor fan. The heat recovery system dramatically lowered the compressor discharge temperature, reducing the load on the dryer by 70 percent.
Because the demand for hot water was concentrated in a 6-hour period at night, we also designed and built a thermal storage system consisting of a highly-insulated 3500 gallon holding tank with variable speed drive duplex pumping system to store the steady hot water production from the air compressor and deliver as needed throughout the day.
Our unique design provided free hot water to the Cains wash-down and CIP process loads. For the remainder of the load, not provided by the compressor, we installed on-demand condensing hot water heaters operating at 95% efficiency.
This fully integrated system was stocked with leading edge technology centered around an Allen Bradley PLC programmed to maximize system efficiency: full instrumentation, automatic pumping changeover, thermal backup, level and temperature monitoring and control.
Results
Implementation of IMEC’s solution resulted in annual gas and electrical savings of more than $50,000 per year. IMEC personnel managed the incentive process with National Grid and Cains received $103,000 in utility rebates. In addition, CIP and sanitation time was dramatically reduced.
The project was honored as the 2015 Innovative Project of the Year Award by the Association of Energy Engineers of New England (AEENE).
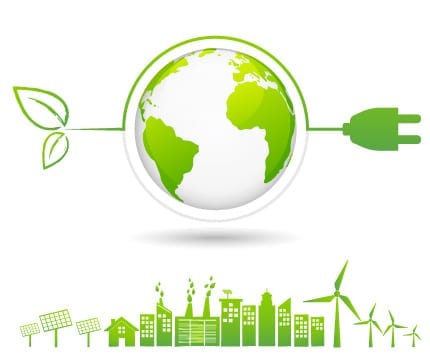
Interested in More Information About How IMEC Can Save Improve Your Energy Efficiency?
Our engineers can dramatically improve your plant efficiency and help you take advantage of utility company rebates to cover a portion of the cost. Learn if our scientific approach to engineering is right for you. Contact us for a complimentary energy efficiency evaluation.