Energy Efficiency Case Study
Air compressor heats multiple water systems at Smith’s Medical
Award-winning system: recognized as the year’s Best Compressed Air Energy Project by the Association of Energy Engineers (AEE), New England Chapter
Energy-efficient compressor and heat recovery skid system yields 1.88 year ROI.
System Highlights
- The old compressor was located on a mezzanine, which required a structural engineering evaluation.
- The new compressor is an Atlas Copco Z Oil-Free with Variable Speed Drive (VSD).
- IMEC also constructed a single heat-recovery skid with state of the art PLC controls, single point connections, and quick ROI.
- This system solved a challenging HVAC issue: in the past, the fresh air to the existing air compressors was drawn from the plant, adding to HVAC load during summer. The existing compressors were consuming huge amounts of conditioned air. By employing a water-cooled design, our system took advantage of reclaiming wasted heat from the air compressor, which: 1) added heat to the HVAC/hot water loop, 2) preheated water for their steam generator, and 3) preheated the boiler feed water.
- The project included a $200,000+ rebate incentive from the electric utility. Total fuel and power savings amount to more than $200k annually, with an exceptional 1.88 year simple payback.
Systems Engineered For Maximum Operating Efficiency
The equipment recommendations on the project were made with an eye on maximizing the energy efficiency and included the Atlas Copco Z oil free sir compressor package with Integrated Variable Speed Drive. The compressor system is a 250kW (330 HP) model ZR250VSD with a capacity of 1,527 CFM (FAD) @ 100 psig. It employs an on board microprocessor to monitor system pressure and maintain set point within 1.5 psig. The integrated VSD insures that the kW consumption of the compressor directly matches the system demand. A custom stainless steel remote intake was installed, increasing efficiency by an average of 5%. Overall power savings compared to the existing legacy system are extraordinary at more than $90,000 annually.
Carbon Zero Energy Recovery
The Carbon Zero option was integrated to lower energy costs to the absolute lowest level. With this configuration, the heat generated during compression is converted into usable hot water with temperatures between 180-190F. In this installation, the free hot water is used in the HVAC heating, preheating the water used in the steam generator and the boiler feed water. The reduction in oil consumption yielded savings of approximately $60,000.00 annually. Additional savings by reducing the HVAC heat load produce approximately $50,000.00 in savings annually.
It is important to note that this option eliminated the need for a separate Dry radiator and associated pumping skid required for cooling the equipment (estimated at $100,000.00).
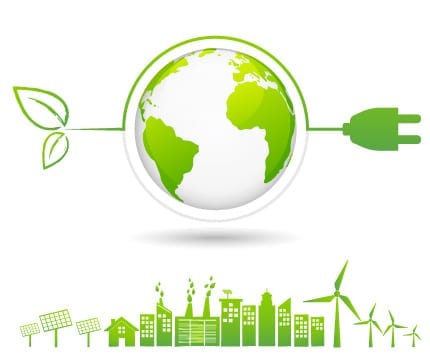
Interested in More Information About How IMEC Can Save Improve Your Energy Efficiency?
Our engineers can dramatically improve your plant efficiency and help you take advantage of utility company rebates to cover a portion of the cost. Learn if our scientific approach to engineering is right for you. Contact us for a complimentary energy efficiency evaluation.