Energy Efficiency Case Study
Comprehensive Heating System Overhaul Reduces NH Plant’s Carbon Footprint by 50%
“IMEC’s level of commitment is exceptional. The company never stops thinking, and their process and approach is first class.”
— Dean Laughy
General Manager
Freudenberg-NOK
The project has reduced energy costs by more than $1,100,000 per year at the Freudenberg-NOK plant in Bristol, NH
IMEC recently completed a comprehensive multi-million dollar overhaul of a steam heating system at the Bristol, NH facility of Freudenberg-NOK Sealing Technologies. The global manufacturer is committed to environmental sustainability and was looking for a new heating system that would not only reduce the plant’s carbon footprint but keep its employees more comfortable during cold New Hampshire winters.
The creative engineering design addressed many functional inefficiencies of the previous system:
- a substantial plant air negative condition,
- heating, cooling, and production controls, and
- excessive maintenance costs. Problematic regulatory issues were also eliminated, including #6 fuel emissions, on-site fuel storage, and boiler certification requirements.
The old system, which had employed obsolete high-pressure steam boilers and #6 fuel oil, was scrapped in favor of efficient, leading-edge liquefied natural gas (LNG) technology, initially phased in by employing propane as a bridge fuel
Energy Savings
- Projected fuel savings of $1.1 million annually
- Electrical savings of $70,000 per year
- Plus 50% carbon footprint reduction with total carbon emissions from the facility reduced by an extraordinary 4,000 tons per year
System Description
All of the production requirements, formerly served by steam, were converted to operate with hot water. IMEC designed and installed a high-efficiency 6 million BTU hot water boiler system with VSD pumps and microprocessor controls to provide the primary heat source for production.
34 rooftop units, previously utilizing DX air conditioning and either steam or electric heat, were replaced with new high-efficiency gas-fired HVAC units. The waste heat from the factory’s air compressors is also being utilized.
To capture the 1,200,000 BTU/HR available from the existing air compressors, IMEC designed and installed a custom heat recovery coil that takes advantage of the available glycol temperature and converts it into usable heat. Select units in the factory were retrofitted with these coils. The coils are now the primary source of heat, augmented with gas heat when the heating requirements increase. This approach maximizes the number of hours per year of “free heat.”
Using the heat from the air compressors has also reduced the load placed on the air compressor’s cooling tower, which results in lower cooling energy usage, evaporative water usage, and chemical treatment costs.
In addition to the energy and maintenance savings, climate control in the factory and offices have significantly improved employee comfort.
“It’s a big deal for Freudenberg to reduce one of our plant’s carbon footprint by 50% while simultaneously creating a far more comfortable environment for employees.
“IMEC was a great business partner. The project started with a smart engineering solution. From there, the execution was essentially flawless: all of the conversions we’ve done—34 pieces of process on the floor, and 37 rooftop units—were accomplished without any loss of downtime.”
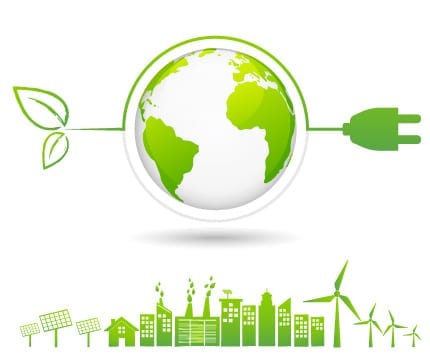
Interested in More Information About How IMEC Can Save Improve Your Energy Efficiency?
Our engineers can dramatically improve your plant efficiency and help you take advantage of utility company rebates to cover a portion of the cost. Learn if our scientific approach to engineering is right for you. Contact us for a complimentary energy efficiency evaluation.