Energy Efficiency Case Study
Home Market Foods increases oven production capacity with IMEC
The project will cut Home Market’s energy costs by $240,000 per year.
The Challenge
Like many customers, Home Market Foods, a growing specialty provider of fully cooked and frozen meals, needed to respond to growing demand by increasing production capacity at its plant in Norwood, MA. Expansion plans included the installation of new ovens requiring High Pressure Steam and five additional hose stations that exceeded the system’s hot water capacity. Exhaust air from the ovens is directed to a Regenerative Thermal Oxidizer (RTO).
Solution
Our solution addressed initial needs while providing the built-in option for future expansion. To satisfy high-pressure steam demand, we engineered an On-Demand Modular High Pressure Boiler system with built-in economizers, featuring two 150HP Miura boilers. All facets of the system design and components account for the future addition of a third boiler.
Hot water needs were addressed by retrofitting both the company’s existing low pressure and high pressure systems. A new EZ Heater was added to the low and high pressure systems. In combination, the two systems provide a total of 470 GPM with the potential third boiler increasing the capacity to 585 GPM. Hot water is directed to a new 3,000 Gallon insulated storage tank. A pump station, located next to the tank, contains duplex high pressure and low pressure pumps, offering 100% redundancy in the hot water delivery system.
A new recirculation line ensures uniform tank temperatures, and bladder tanks are used to maximize the pumps’ operating efficiency.
An economizer interfaces with the exhaust stream on the Regenerative Thermal Oxidizer (RTO) to capture the waste heat. Capturing this heat to supplement hot water generation and preheat the boiler feed cuts gas usage by approximately 175,000 Therms/year. In combination with the new high efficiency Miura boilers, total system savings are 241,700 Therms annually.
System Benefits
- Increased production capacity
- Reduced sanitation time
- Reduced water consumption
- Increased reliability and lower maintenance cost
- Project cost 1.4 million, utility rebate ($650,000), net cost $750,000
- $240,000 annual gas savings each year
- 3.125 year ROI
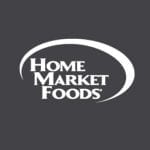
“My sense is that no challenge is too great for IMEC. They were adamant that they could solve our unique problem, and they completely met our expectations.”
—Sokly Saing, Production Engineering Manager, Home Market Foods
“There are many things to like about IMEC’s process and people. They’re transparent about their approach and solutions; nothing is unsaid or mysterious. We could get an answer to questions at anytime, and once we became comfortable with their expertise and focus, we didn’t have to worry about the work moving along successfully without our oversight.
This production expansion project would have been very challenging for most other firms. They enthusiastically embraced the challenge and conceived and executed a great solution.”
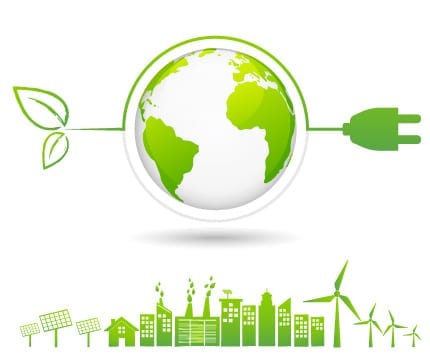
Interested in More Information About How IMEC Can Save Improve Your Energy Efficiency?
Our engineers can dramatically improve your plant efficiency and help you take advantage of utility company rebates to cover a portion of the cost. Learn if our scientific approach to engineering is right for you. Contact us for a complimentary energy efficiency evaluation.