Energy Efficiency Case Study
Increased production speed/capacity results from unique application for Brand Aromatics, a division of McCormick Spices.
Project Challenge
The New Jersey production facility of Brand Aromatics, a division of McCormick Spices, had been using a chiller system with a large glycol storage tank to cool 500-gallon kettles used for cooking broth.
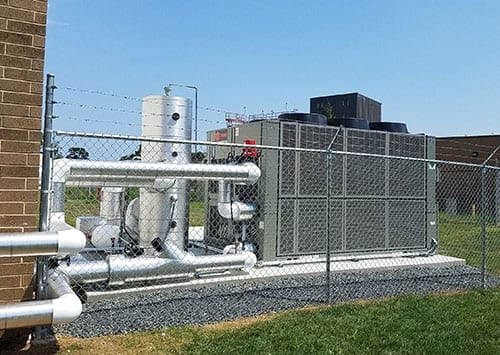
Overview
The original goal was to increase capacity. In the analysis process, our team discovered numerous other issues. When cooling was initiated, the broth temp is at 200°F, created an extremely high load which shocked the system and occasionally would shut down the chiller. This existing system required a gigantic amount of cold glycol in reserve to handle the initial surge.
In addition to increasing capacity, the customer desired to cool multiple kettles simultaneously. Because multiple kettles would now be in various stages of the cooling cycle, the large reserve glycol system would no longer work. The ultimate solution needed to proportion the available cooling to the individual kettle cooling processes.
This project was a classic example of a customer having a unique multifaceted problem without an obvious solution, which is always a challenge we embrace.
Solution
Our engineering team collected data from the cooling of several batches of broth, analyzed the heat transfer rate, and then designed a system that modernized the process with sophisticated controls integration. The existing air-cooled chiller was integrated with a new air-cooled low-temperature chiller. The pump skid incorporated primary and backup pumps with digital controls to sequence properly with the chillers and a buffer tank to reduce load fluctuations on the chiller.
Controls were a crucial component of the system, as many load and temperature fluctuations needed to be monitored and controlled to ensure proper uninterrupted operation. The controls limit and ration the heat extracted from the kettles to match what the chiller can manage. The system also monitors several aspects of the operation and makes real-time adjustments, both local and on the floor, to maintain system operation.
In all, the system is designed to cool 10,000 pounds per hour of product at maximum capacity with optimal cool down efficiency and zero system downtime. The process now attains final cooling temperature 25% faster.
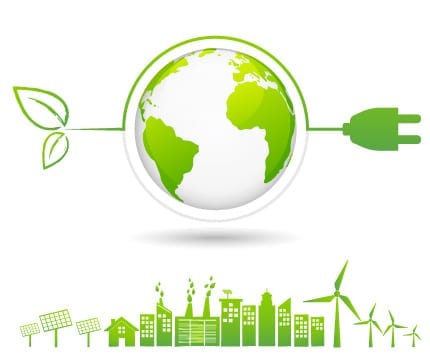
Interested in More Information About How IMEC Can Save Improve Your Energy Efficiency?
Our engineers can dramatically improve your plant efficiency and help you take advantage of utility company rebates to cover a portion of the cost. Learn if our scientific approach to engineering is right for you. Contact us for a complimentary energy efficiency evaluation.