Energy Efficiency Case Study
Saint-Gobain Powerhouse Refurbishment Project–Air Cooled Condenser Unit
System Benefits
- Increased plant power output from 3 megawatts to 6 megawatts
- Reduced condenser fan energy by 250,000 kWh or $30,000 per year
- Utilization of gravity condensate return eliminated 7 ½ HP duplex pumping station
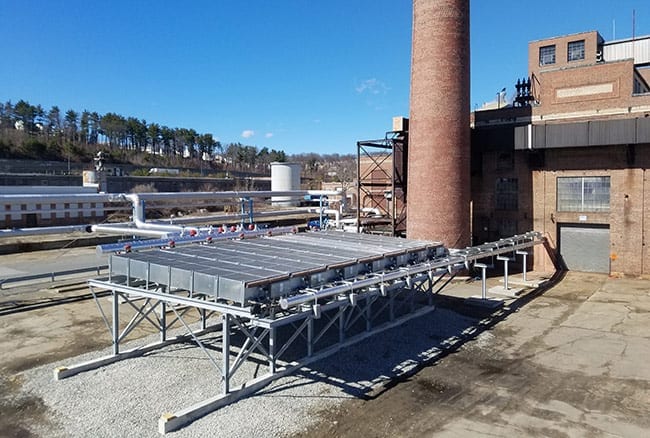
Project Challenge
Repeat customer Saint Gobain Abrasives in Worcester, MA initiated an upgrade of its onsite Powerhouse facility with the goal of increasing current generating capacity. The design and installation of an Air Cooled Condenser Unit (ACCU) was needed to condense exhaust steam from the steam turbine during warmer months, and return condensate to the boiler without water loss.
The Solution
IMEC engineered and installed an ACCU with a capacity of 100,000 lbs/hour of steam. The exhaust steam from the turbine was directed to a manifold feeding seven individual condenser coils.
As a result, ambient air now provides the required cooling for condensing. After condensing in the coils, the condensate is directed to a header and then gravity fed to the condensate tank in the mechanical room.
The existing condensate return tank was outfitted with new pumps utilizing Variable Speed Drives (VFDs) to return the condensate to the boilers.
An Allen Bradley PLC controls the entire system with a remote HMI located on the turbine deck. The system controls the speed of the condensate pumps to maintain tank level. The flow of steam to the condensers is modulated to maintain the proper pressure in the main header. The PLC also controls the number and speed of fans operating to maintain the desired back pressure at the condenser.
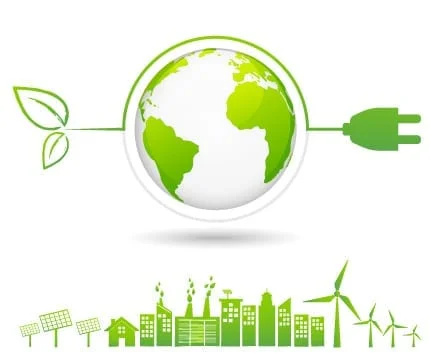
Interested in More Information About How IMEC Can Save Improve Your Energy Efficiency?
Our engineers can dramatically improve your plant efficiency and help you take advantage of utility company rebates to cover a portion of the cost. Learn if our scientific approach to engineering is right for you. Contact us for a complimentary energy efficiency evaluation.