Energy Efficiency Case Study
Centralized cooling system, exhaust heat recovery for NuWay Tobacco
After electrical and gas incentives from Northeast Utilities, projected payback/ROI was just 2.57 years, with annual savings of $137,250 per year.
Project Description
NuWay was involved in a planned expansion to add a fourth production line and approached IMEC with a request to provide additional cooling to serve the new line. IMEC performed a comprehensive audit of the existing cooling system. The audit identified several potential areas of savings including the cooling towers, chillers, and heat recovery.
IMEC engineered solutions provided the following benefits:
- Reduce energy consumption of the cooling tower system by replacing the existing four cooling towers and pumping systems with a single two cell high efficiency tower and complementary duplex 40 HP VSD pumping skid, capable of handling the entire cooling load of the factory including the new expansion.
- More precise temperature control was achieved by replacing the existing line spray system which utilized several pumps, tanks and manual controls with a custom designed tank, pump and valve assembly which delivered precise temperature and pressure for the cooling sprays. In addition to reducing horsepower and energy a consistent temperature and pressure yielded higher quality product with less scrap.
- Energy savings in the chilled water portion of the process was achieved by replacing the existing air cooled 50 ton reciprocating chiller with a York high efficiency, water cooled, 60 ton screw chiller. Condenser cooling was handled with the new central cooling tower. The existing chiller tank which utilized both a chiller pump and loop pump was replaced with a duplex variable speed drive pumping skid utilizing a single pump to handle the chilled water process.
- The new paper line continuously flows 20,000 CFM of outside air over the product. The air is split between the rear and front sections of the line and is heated to approximately 160°F. After treating the product the air is exhausted to the outside. IMEC designed and built heat exchangers and installed them on the roof at the two inlet and discharge ducts. The system was able to reclaim 80% of the exhaust heat and use it to preheat the inlet air.
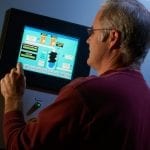
“The cooling system has been everything they promised.”
—Rick Gendreau, Plant Engineer, NuWay Tobacco
“When I first met with IMEC, I was looking to have them provide additional cooling for our new line. IMEC looked at our entire system and proposed installing one large efficient tower for the whole plant, replacing our air cooled chiller with a more efficient water cooler chiller, designing a more efficient spray system for our lines, and installing heat recovery in our new line 4 process. They worked with Northeast Utilities to secure over $350,000 in utility rebates for us. The rebate and energy savings made spending the extra money a no brainer. The installation was smooth and on schedule. An added bonus has been the improvement in our product quality.”
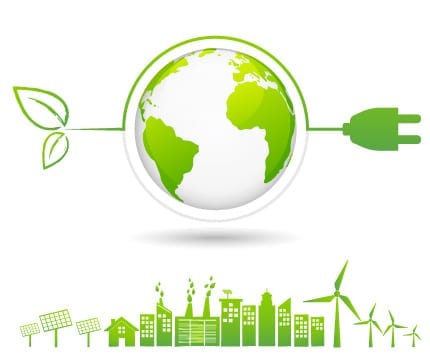
Interested in More Information About How IMEC Can Save Improve Your Energy Efficiency?
Our engineers can dramatically improve your plant efficiency and help you take advantage of utility company rebates to cover a portion of the cost. Learn if our scientific approach to engineering is right for you. Contact us for a complimentary energy efficiency evaluation.