Energy Efficiency Case Study
Hydraulic pumps heat building at Dirats Laboratories
The project yielded $60,000 per year in energy savings.
“The guys at IMEC are smart. Their design solution was intelligent and effective, with brilliant simplicity.”
—Eric Dirats, President, Dirats
Project Description
Dirats Laboratories in Westfield, MA performs materials and metals fatigue testing, primarily for the aircraft industry. They were involved in a planned expansion and approached IMEC with a request to replace the process cooling equipment serving their hydraulic power supplies. The company was interested in energy efficiency and inquired if there was a way to use the heat generated, perhaps by heating the supply to his water source heat pumps. IMEC undertook the project as a design –build and the results were a comprehensive revamping of the HVAC and process cooling in the facility.
The waste heat from the plant production equipment is captured and now heats the entire building. Substantial savings were also achieved in the cooling mode, not to mention precise environmental temperature control in the production area and improved comfort cooling for office personnel. Finally, we virtually eliminated the use of city and well water for cooling in the production area. The details of our assessment are as follows:
Initial Assessment
The original system consisted of a water loop feeding the 24 Water Source Heat Pumps (98.5 Ton total) in the main facility. This loop was heated with a 119 kW Electric Boiler and cooled with a four (4) cell Closed Circuit Cooling Tower as required. The full load cooling required was approximately 1,200,000 BTU/H. A new building addition added a total of 40 Ton Water Source Heat Pumps which added 480,000 BTU/H.
The existing Hydraulic power supplies for metals fatigue testing were cooled through a combination of city water, well water and a BAC Closed Circuit Cooling Tower circulating Propylene Glycol. The entire hydraulic load is 477.5 HP and the diversity factor is estimated at 65%, representing a heat rejection of approximately 789,905 BTU/H.
The Laboratory testing equipment employed a total of eight (8) air cooled chillers which dumped heat directly to the space. Three (3) Heat Treat ovens were plumbed using city water. This equipment has a combined heat rejection of 307,350 BTU/H. The total cooling load is approx. 2,780,000 BTU/H
Secondary issues to address:
• The existing Heat Pump Closed Circuit Cooling Tower was excessively loud.
• To maintain steady ambient temperatures in the facility (72° F to 78° F).
Analysis & Recommendation
The expansion project offered us the opportunity to centralize the cooling system. We designed a single cooling system which employed a closed circuit evaporative cooling tower with a duplex VFD pumping skid. The system we installed is rated for 3,000,000 BTU/H and provides cooling for all the Hydraulic Power Supplies as well as the Heat Pumps, and chillers. The piping loop was reconfigured to capture the heat rejected from the Hydraulics for the Heat Pump loop.
The Primary Benefits
- Reduced energy cost. Utilizing an efficient centralized system and reclaiming the heat rejected from the heat pumps yielded substantial energy savings in both the heating and cooling modes. The lower tower temperatures increased the efficiency of the heat pumps in the cooling mode and the 775 MBH reclaimed from the hydraulics and chillers eliminated the electric boiler in the heating mode. Using a central water cooled cycling chiller eliminated the eight (8) individual air cooled chillers. This configuration improves chiller performance and reliability, and eliminates the additional AC load in the cooling months. We estimate a total savings of $60,000.00 annually.
- Simplified and reliable operation. The system is designed to be totally automated to simplify operation and provide stable and reliable temperature control. The evaporative spray pump and VSD cooling fan is thermostatically controlled and the system is designed to provide maximum cooling water feed temperature of 85°F. A three way control valve will automatically by-pass the tower in cold weather to prevent heat loss and stabilize the loop temperature.
- Reduced maintenance. The system is a closed circuit system and employs Propylene Glycol loop to eliminate the possibility of freezing. Due to the inherent cleanliness of the closed circuit system, one of the additional benefits is the elimination of all heat exchanger maintenance.
- Eliminated City water and Well water usage
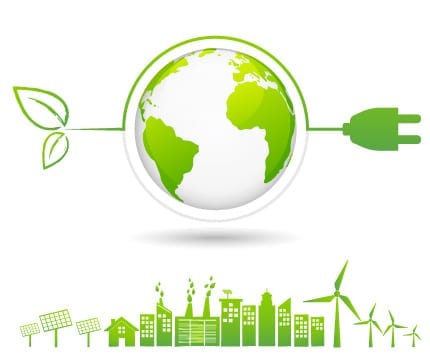
Interested in More Information About How IMEC Can Save Improve Your Energy Efficiency?
Our engineers can dramatically improve your plant efficiency and help you take advantage of utility company rebates to cover a portion of the cost. Learn if our scientific approach to engineering is right for you. Contact us for a complimentary energy efficiency evaluation.