Energy Efficiency Case Study
Three energy-saving projects produce monster results for Vitasoy/Nasoya
Project Overview
Vitasoy’s boiler plant consisting of 350 HP and 125 HP high pressure boilers was inadequate for the resultant load of an imminent plant expansion. IMEC was asked to survey the plant and devise a solution to reduce the load on the boilers and eliminate the need for additional boiler capacity.
Solution
Extensive metering and measurements revealed the boiler loading was not consistent but had many peaks and the steam required varied greatly. IMEC discovered the high demand was concurrent with the CIP and wash down operations as steam is used as the energy source for both of these processes.
IMEC’s solution was to create the plant hot water directly with gas and use that hot water to supply the needs of the high temperature CIP. The usage profiles and peak demand dictated a hot water system designed with ample capacity and storage to meet the fluctuating requirements of the facility.
We built and installed a large 3,500 gallon insulated stainless steel hot water storage tank. The package included variable speed duplex pumping to manage the spikes in demand and supply the hot water to the plant floor at a constant optimal pressure. Hot water is produced utilizing condensing on-demand 95% efficient hot water heaters. Modulating mixing valves ensured the hot water was delivered to the points of use at the proper temperatures.
During the walkthrough, we identified other energy saving projects:
The first was related the electric heat pump hot water system serving the bean soak and grind operation. Due to the unit’s controls, it ran consistently in hot gas bypass (a condition of false loading) and repeatedly on its resistive back up heat to maintain sufficient capacity. The new hot water system’s capacity allowed this load to be transferred off the heat pump unit.
The second was associated with a large 40,000 cfm gas dryer. The dryer is a continuous throughput type unit which draws in fresh ambient air, heats it to 350°F, then exhausts the moisture laden air at 180°F. Due to the nature of the drying process, no exhaust air was recirculated and all air run through the dryer was brought in from the outside. We implemented a dual coil glycol loop to extract heat from the exhaust air stream and introduce that heat to the incoming air stream. By pre-heating the air coming into the dryer, the load on the gas burner is reduced.
Results
By reducing the load attributed to CIP and hot water production, the existing boiler capacity was sufficient for the plant expansion. The hot water storage system provides a constant water flow and pressure to the manufacturing floor. This stabilization in the hot water temperature and supply has reduced CIP and wash down times as well as overall water usage.
The combination of the new hot water system efficiency and the recovered heat in the drying process saves Vitasoy 175,000 therms and 167,000 kWh per year. IMEC personnel managed the incentive process with National Grid. In addition to $188,000 savings per year in energy costs, Vitasoy received utility rebates totaling $553,000.
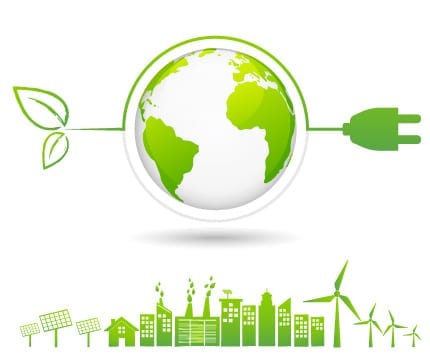
Interested in More Information About How IMEC Can Save Improve Your Energy Efficiency?
Our engineers can dramatically improve your plant efficiency and help you take advantage of utility company rebates to cover a portion of the cost. Learn if our scientific approach to engineering is right for you. Contact us for a complimentary energy efficiency evaluation.