Energy Efficiency Case Study
Heat Recovery System Yields 32% Annual Energy Savings and 42% Utility Rebate at Duncan Galvanizing
The Challenge
The galvanizing process at Duncan Galvanizing’s facility in Everett, MA requires the zinc contents of a large galvanizing tank to be heated non-stop, year round. If the material is allowed to cool, it will solidify. Re-liquefying the zinc takes a lengthy amount of time and the solidified contents can damage the tank.
The forced induction fan for the burners moves approximately 2,000 scfm of 1200°F air through the flue. This substantial non-stop heating requirement offered an ideal opportunity for an energy-saving heat recovery application.
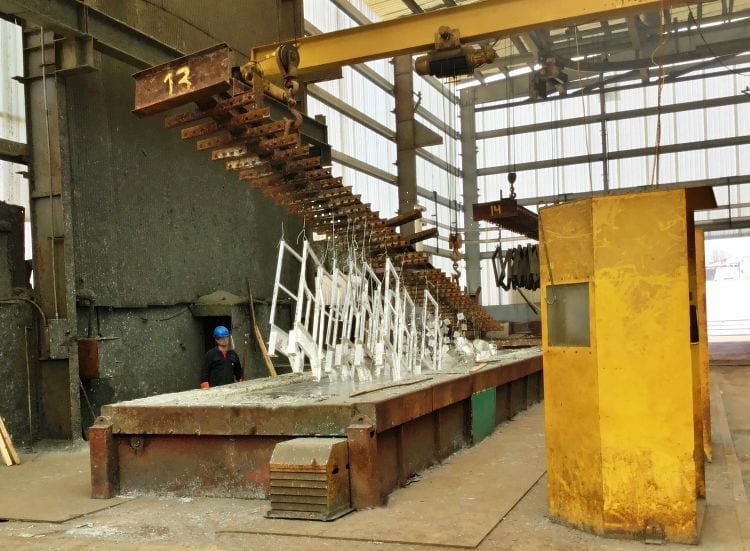
We Recommended Four Improvements
HEAT RECOVERY
In addition to the galvanizing tank, the facility uses natural gas to fire the hot water boiler used to heat eight pre-treatment tanks. The relatively high temperature requirement for the galvanizing tank produces high thermal quality flue gases. We recommended recovering this lost heat and transferring it to reduce the load on the boiler system.
Our system uses a fan that draws exhaust from the main flue and blows it through an air-to- water heat exchanger. A damper system on the suction side of the fan maintains acceptable temperatures to the coil and fan to avoid overheating. The boiler water is circulated through that coil to recover the heat. The boiler is used to trim up when necessary.
INSULATION
The second energy-saving measure related to the hot water piping insulation, which was worn or nonexistent. Using the DOE’s insulation heat loss calculator, we determined the heat loss for the bare pipe and the proposed insulated pipe. We recommended installing 1″ insulation on the piping around the tank area on approximately 160′ of 3″ pipe, eliminating 75% of the heat loss.
HEATED CAUSTIC TANK
The third recommendation involved the heating of the Caustic tank, which is kept hot using a designated Gas Burner system. We recommended installing a Titanium heat exchanger to utilize the heat from the heat recovery system.
TEMPERATURE CONTROL SYSTEM
Our fourth recommendation was to replace the existing manual system with a new temperature control system employing thermocouples to monitor the tank temperature. A Process Controller will allow individual set points to adjust the amount of flow required for each tank to maintain temperature. Modulating ball valves and circuit setters will balance the hot water flow through the various tanks.
Efficiency & Financial Results
Existing gas usage totaled approximately 280,000 therms, annually. Estimated savings of approximately 80,000 therms per year amounted to 32% of the total process gas load. IMEC also managed the energy rebate incentive process, resulting in an impressive 42% project rebate from NGrid.
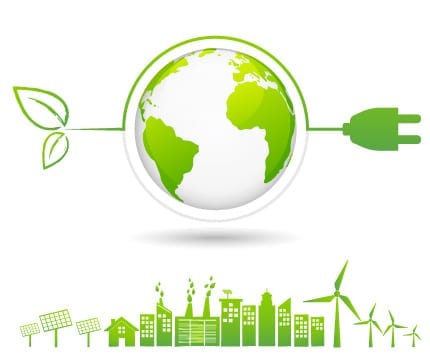
Interested in More Information About How IMEC Can Save Improve Your Energy Efficiency?
Our engineers can dramatically improve your plant efficiency and help you take advantage of utility company rebates to cover a portion of the cost. Learn if our scientific approach to engineering is right for you. Contact us for a complimentary energy efficiency evaluation.